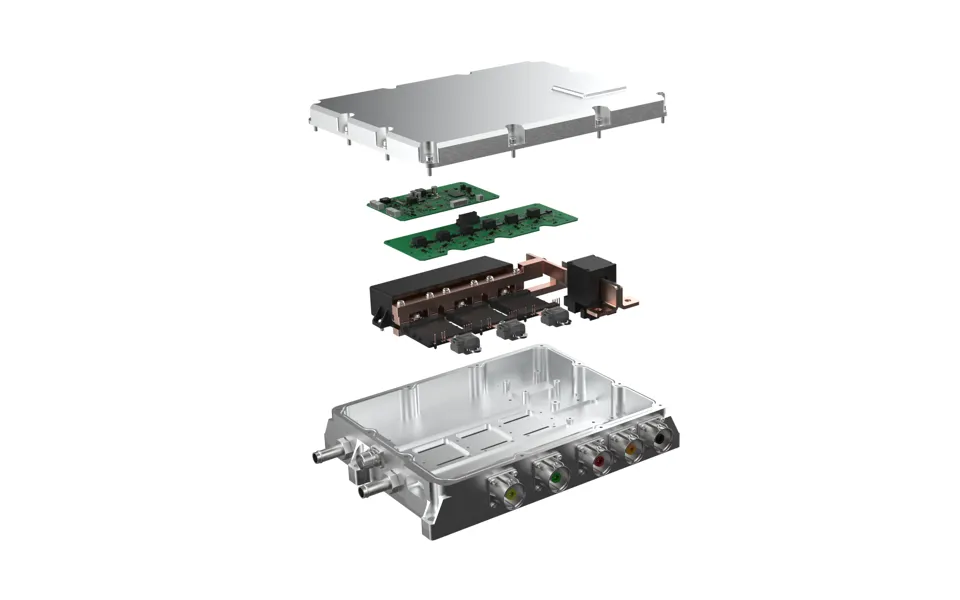
Developing Trends & Challenges for SiC Based Power Inverters
24 Mar 2023
As electric vehicles (EVs) grow in popularity, innovative technologies must be developed to meet the rising energy demand by significantly increasing system efficiency, reducing size and weight, and extracting the maximum benefit from expensive battery packs. Since technology in the EV space is advancing at such a rapid pace, companies must implement an efficient strategy to gain a head start in planning and an edge over competitors.
Inverters are a critical part of the electric vehicle drivetrain. An inverter is similar in function to a “fuel control system” of a conventional vehicle, but for electric vehicles. The inverter controls when and where current flows in the motor to efficiently control motor torque and speed. All the electrical power and energy delivered to the motor must first flow through the inverter, so inverter efficiency is extremely important to overall vehicle efficiency to maximise vehicle range, productivity, and utilisation factor.
Technical, economic, and environmental drivers are three of the main forces behind advancing SiC based power electronics. From a technical standpoint, SiC power electronics development is focused around reducing the size and weight of systems. This will include advancements in lowering power loss, high frequency operation, higher junction temperature and higher voltage operation. When it comes to an economic driver, the key benefit of SiC inverters is a reduction in operational costs stemming from higher efficiencies. Operating an electric vehicle at higher efficiency translates to greater range. And finally, when you’re talking about the key environmental driver of SiC based power electronics, the transition to electrified systems to reduce CO2 is being driven by SiC systems because of the inherent technical and economic benefits of SiC that provide higher system efficiencies and more compact solutions. Operating the electric vehicle at higher efficiency means that the energy usage is better. Charging energy may come from fully green sources like solar panels or wind power, and therefore, minimizing wastage in the form of heat is very important.
Innovation around inverter technology has been advancing rapidly. The technology has evolved from Insulated Gate Bipolar Transistors (IGBTs) to Silicon Carbide as a response to size and weight considerations. SiC inverters provide reduced operational costs, are smaller and lighter, and are more efficient because they can handle higher voltage architectures. This in turn allows vehicles to be lighter and increase charging rates, helping to expand the adoption of an electrified mobility solution. Advancements in the electrification architectures are driving systems upwards to improve vehicle performance compared to 400V through greater range, higher charging rates and lower vehicle weight. Therefore, 800V and higher architectures results in greater vehicle productivity.
Over the next decade, innovations in SiC will continue to focus on overall system weight and size reductions to achieve even greater power density as well high(er) efficiency for overall improved system operational costs. SiC fabrications will grow and processes will improve to maximize throughput; wafer sizes will also increase to 200mm or larger, which should result in cost reduction. When it comes to forecasting market demand over the next 10 years, the transition to electrified systems will continue to accelerate and expand across numerous applications in different markets. If production costs of SiC wafers comes down through process improvements and upscaling, then there will be a larger penetration into the EV market.
However, SiC inverter development is a costly, risky, and time-consuming venture even for the most advanced companies. Anywhere from 2.5-3.5 years of development time from concept to production sample is typical, requiring a wide range of skills and resources for complete development. Coupled with manufacturing and throughput challenges at the SiC wafer level, which keeps prices high and therefore supply chain availability remains tight. At the power module level the technology is now reliable and efficient, particularly at high voltages >600V where it is unmatched, though GaN technology is catching up and providing a compelling alternative for applications <600V and <100kW where it may continue to be a more manufacturable and cost favorable alternative. Specific cost benefits between GaN and SiC depends on application duty cycle and switching frequency. Ricardo’s team of experts can help to determine whether applications are better suited for SiC, GaN or Si IGBT (incumbent technology).
In summary, SiC inverters are smaller and lighter, enabling engineers and designers to take advantage of aerodynamic and packaging improvements and reducing the amount of cooling a vehicle requires. The global market for SiC power devices is forecasted to grow tremendously over the next decade, and with such fast advancements in this space, it is very important for a company utilizing this technology to comprehend the patterns of the market movements, manufacturing and throughput challenges, and developments with manufacturing technologies. An efficient strategy is critical to gain a head start in planning and an edge over competitors.