
Liquid hydrogen: how can we harness its benefits safely?
14 Sep 2023
Written by Stuart Devereux, Hydrogen Safety and Response Associate Trainer at Ricardo, and Hector Wilson, H2 for Mobility, Energy Transition & Sustainability Operations Lead for Air Products
Introduction
As one of the most abundant elements on the Earth, hydrogen offers real potential as one of the most sustainable energy carriers. For the global transport, energy and heavy industry sectors, hydrogen could be a key enabler in achieving the Paris agreement targets and help to decarbonise manufacturing processes such as cement, plastics, ammonia and steel which remain heavily dependent on fossil fuel.
In order to be usable in this way, hydrogen must be extracted, either from water (H2O) or fossil fuels like methane (CH4). This extraction requires energy and a subsequent storage solution. Currently, three storage systems are available: compressing the gas and storing it in high pressure gas cylinders; cooling it as liquid hydrogen; or storing it within solid structures called metal hydrides.
With more than 100 years of engineering experience in improving mobility efficiency and over 60 years of leading-edge expertise in delivering environmental and energy solutions, Ricardo is uniquely placed to guide clients who are looking to hydrogen to decarbonise challenging energy, industrial or transport applications. In this article, industry experts from Ricardo, share their insights on some of the properties of liquid hydrogen, the challenge of cooling temperatures and its safe storage issues, while experts from Air Products, a hydrogen producer, discuss how they safely approach use and storage of the gas.
Properties of liquid hydrogen – insights from Ricardo’s safety expert
Liquid hydrogen is lighter than water: 1m3 of liquid hydrogen only has a mass of 70kg. It is transparent with a light blue tinge. On expanding back to a gas, it increases in volume 845 times and does so very rapidly, but its most important property is its extremely low boiling point.
Hydrogen needs to be cooled to -253oC to liquify. By comparison, the air around it will become solid as oxygen freezes at -218oC and nitrogen at -209oC. What this really means is that air will condense on any cold surfaces which are not insulated, producing what looks like regular water droplets but which are in fact heavily enriched with oxygen, increasing the flammability and oxidation risks. For example, a liquid hydrogen spill onto a bituminous tarmac surface results in an increased fire risk because the fuel and oxygen are readily combined.
The fact that we can liquefy a gas means that there are attractive forces between gas molecules. These forces are not large and are only effective over very short distances. Liquefaction of a gas occurs when the attractive forces dominate over the energies of the gas molecules. To bring the molecules close together, pressure needs to be applied. However, as the temperature of the gas is raised, the energies of the molecules increase, and can overcome the attractive forces between them. Finally, a temperature is reached where no amount of pressure can keep the molecules close enough for the attractive forces to be effective and the gas will no longer liquefy. The highest temperature at which a gas liquefies is called its critical temperature and the critical pressure is the pressure required to bring about this liquefaction at the critical temperature.
For hydrogen the critical temperature is -240oC and critical pressure is 12.8 bar. If liquid hydrogen warms up from -253oC as far as -240oC then no amount of pressure will keep it in its liquid state. It will behave as an ideal gas and expand rapidly, a property that has consequences for how liquid hydrogen must be stored.
The flashpoint (the temperature at which the fuel generates sufficient vapours to facilitate a flame given an ignition source) for hydrogen is -231oC, which is the lowest temperature compared to other fuels.
So how do you cool hydrogen to -253oC?
Gas |
Inversion temp at 1 bar |
Hydrogen |
195K or -78oC |
Helium |
45K or -225oC |
Nitrogen |
621K or 348 oC |
Oxygen |
764K or 491 oC |
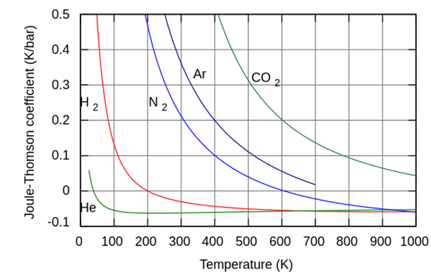
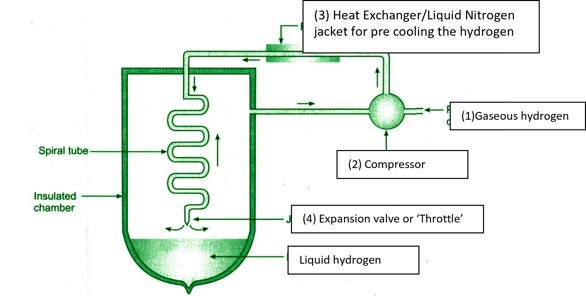
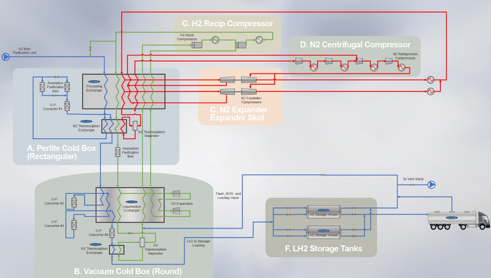
A hydrogen producer’s approach – Air Products
Air Products is the world’s largest hydrogen supplier and has more than 60 years of experience of safely producing, storing, handling and distributing hydrogen to market. The company has an unsurpassed safety record having earned more safety-related awards than any other industrial gas company and have taken a leadership role in supporting the hydrogen fuel community in the safe use of hydrogen.
Air Products’ experience in the hydrogen for mobility market, through its work on a liquid hydrogen store and bulk trailer in Ghent, Belgium, indicates that liquid hydrogen technology brings significant advantages in terms of reliability, footprint, and scalability.
While a small fleet conversion using 500kg or less of hydrogen warrants gaseous hydrogen as the right solution, for larger fleet conversions a liquid hydrogen tank presents the best option and operates much like a diesel storage tank.
In addition to supplying a larger capacity, a liquid hydrogen installation is much more space efficient than a gaseous solution.
As part of our work, we have seen significant progress in the hydrogen bus market in terms of sustainable energy supply to vehicle fleets. Our hydrogen bus refuelling stations in the municipality of Hürth in Germany and the Go-Ahead Group near Gatwick in the UK are good examples.
The latter represents the largest renewable bus deployment to date in the UK fuelled (or supplied) by the largest liquid hydrogen-based station in Europe. For this project, Air Products will initially be providing fuel to 20 buses, but the equipment can, in time, support a full depot conversion.
As interest from bus and truck operators continues to grow, part of the conversation must be about the right mode of hydrogen supply. From Air Products’ work supporting clients with the implementation of this new technology, the company knows that safety is the number one priority and all modern hydrogen fuelling stations are designed with numerous safety systems incorporated. The design of the fuelling station includes process software that monitors the station's status, backed up by independent hardware safety instrumentation and safety devices. Dispensers monitor the fueling process in real time and communicate with the vehicle. If the dispenser detects a leak or other anomaly with the fueling event, it will shut off and prevent further fuelling. Flame and hydrogen detectors are deployed at the station to monitor for fires and hydrogen leaks. These systems are designed to shut off the supply of hydrogen in the event of an alarm.
Storing liquid hydrogen: what you need to know
Having converted gaseous hydrogen to liquid hydrogen it is important to keep it that way until back to gas conversion is required. Ricardo’s global expertise and commitments across multiple sectors and industries means the company truly understands the dos and don’ts, challenges, opportunities and risks to implement this technology safely. Despite the best insulation materials, some vaporisation and hence boil-off is inevitable and must be accommodated. With an expansion ratio of 848 a tank full of liquid hydrogen at 1 bar should it convert back to gas would experience a pressure rise to 1720 bar, thus hydrogen can only be stored in self-regulating systems fitted with pressure relief valves or bursting discs.
Boil-off quantities can be influenced by several factors including internal spin alteration, heat leakage, and, sloshing and flashing.
Internal spin alteration of the hydrogen molecules: Hydrogen atoms preferentially join to form a pair to comprise a hydrogen molecule (H2). In ortho-hydrogen, both the hydrogen atoms spin in the same direction. In para-hydrogen, each atom spins in opposite directions. The ratio of ortho:para hydrogen is temperature dependent.
Hydrogen at normal temperatures and pressures is typically 75% ortho and 25% para. However, below -120 oC the concentration of para-hydrogen increases up to 100%. Thus, during liquefaction, there is conversion of 75% of the hydrogen molecules from ortho to para hydrogen. This change in spin direction generates heat within the liquid and promotes boil-off until the conversion has taken place. It is important to allow this ortho to para conversion to take place during the liquefaction process rather than when the liquid hydrogen is in storage.
Heat leakage: Heat leakage from the vacuumed and insulated vessels can be 1% in smaller vessels but 0.06% in larger vessels due to greater surface to volume ratios. Perlite is a common insulation material used in storage vessels.
Sloshing and flashing: Sloshing is due to movement of the liquid while being transported. This generates kinetic energy which is transferred to thermal energy to the liquid in the tank. Flashing is caused by the introduction of hydrogen from a higher-pressure tank into one at a lower pressure. This injection of liquid hydrogen into the body of the liquid in the receiving tank generates thermal energy and again promotes boil-off. Something to note here is that even transferring liquid from one container to another can create a lot of boil-off. It’s not as simple as moving liquid from one tank to the other as you then also need to safely remove the gas produced in moving the liquid and it can easily be >10% of the transferred volume of liquid which will turn to gas.
Safety issues
The dangers of liquid hydrogen fall into three categories: physical (embrittlement, storage tank failure), physiological (cold burns, hypothermia, asphyxiation and respiratory issues) and chemical (ignition and fire).
Direct contact with liquid hydrogen leads to severe burns and/or frostbite. Inhalation of cold vapour itself can cause respiratory ailments. Contact between skin and uninsulated surfaces can also cause the skin to stick and tear.
A large release of liquid hydrogen can lead to an accumulation of liquid hydrogen and solidified air outside a vessel. As oxygen condenses faster than nitrogen due to its higher melting point this solidified air will be oxygen rich. If this mix catches light, it will ignite with a greater amount of energy than gaseous hydrogen alone. A mix of liquid hydrogen and solidified air is also shock sensitive. A mitigating act can be to apply a water spray to the spill site which introduces heat to the accumulation and vapourises it. The ensuing large condensation cloud and potential ice field must, however, be anticipated.
While this is a possible course of action for a spill on the ground it is a dangerous action if applied to a tank or container. Water is capable of entering pipework, freezing and then blocking the pipe. If the blocked pipe is part of a vent stack the vessel is no longer able to release any over pressure. In 1974, during a chemical plant incident, emergency services sprayed water onto the vent stack after a rupture disc blew and subsequently ignited a leak on a 20,000-gallon liquid hydrogen tank. The vent stack became plugged with ice, with no venting facility left, the tank subsequently failed as the remaining liquid hydrogen warmed up and expanded to gas. The below signage was adopted following this incident and many facilities have subsequently started fitted a secondary vent stack should for some reason the primary stack become inoperable.
Air Products liquid hydrogen storage tank showing vent stack and mandatory signage warning not to spray water onto vent stack.
Vapours from liquid hydrogen are very cold and initially are denser than air. They accumulate initially at low level and then horizontally. The hydrogen vapours spread further in low wind conditions. However, as wind speed increases the dispersion increases greatly the safety distances can be decreased.
Overfilling a liquid hydrogen vessel, should it occur, can operate the pressure relief valve which may lead to a liquid hydrogen spill and/or prevent the pressure relief valve operating further due to solidified air blocking it. To add an extra layer of safety, a rupture disk may also be installed on the pressure relief valve line.
The European Industrial Gases Association (EIGA) has recommended several minimum separation distances for liquid hydrogen vessels. According to their list, the separation distances for liquid hydrogen facilities installed in public spaces, near an occupied building, or near combustible liquid or solid stores are 60, 20, and 10m respectively. EIGA also recommends that liquid hydrogen storage vessels are not installed inside buildings and are at least 10m from overhead lines.
Harnessing the benefits
It is clear that liquid hydrogen has enormous potential as an energy carrier for the decarbonised world, but it is essential that for any industries seeking to achieve its undoubted benefits, it is cooled, stored and handled safely, and its hazards understood and mitigated. Recent tragic events highlight the absolute importance for any companies undertaking cutting edge innovation and implementing new technology to be able to demonstrate that they put the safety of their people above all else, and that they are innovating and implementing in consideration of these risks.
No matter how safely planned, implemented and operated a system is, there is always the risk of something going wrong – and the consequences of an incident involving hydrogen would be catastrophic.
As well as the widely known hazards to people, the environment and infrastructure, history shows that a single hydrogen incident will damage public perception. A lack of public adoption of hydrogen as an energy carrier, the reputational damage to its use and further legislation following an incident could result in all our efforts to use hydrogen as a mechanism to decarbonise being futile. Ricardo’s recent project to support Brighton and Hove Buses is a clear demonstration of how safety is the number one priority of organisations on the decarbonisation journey.
Ricardo supports organisations across transport, energy, government and industrial sectors in their transition to hydrogen. From working on the design for a multi-stack fuel cell system solution for the world’s first truly green passenger carrying airline services to implementing hydrogen generation plants and assessing national adoption plans we are global leaders on the enablement of hydrogen.
In support of our commitment to safe enablement as the priority we offer a variety of hydrogen awareness and safety training, and development support. From entry level awareness through to full engineering control assessments, our world-class experts provide the scientific and emergency response at all stages of the journey.
For information on how Ricardo can support you with the safe implementation, use and evaluation of hydrogen applications visit here or contact us.
It is hydrogen suppliers, industries, regulators, emergency services and each individual’s responsibility to ensure that safety is the number one priority when looking to adopt innovative energy technologies.
About Air Products
Air Products is a world-leading industrial gases company in operation for over 80 years focused on serving energy, environmental, and emerging markets. The company has two growth pillars driven by sustainability. Air Products’ base business provides essential industrial gases, related equipment and applications expertise to customers in dozens of industries, including refining, chemicals, metals, electronics, manufacturing, and food. The company also develops, engineers, builds, owns and operates some of the world's largest industrial gas and carbon-capture projects, supplying world-scale clean hydrogen for global transportation, industrial markets, and the broader energy transition. Additionally, Air Products is the world leader in the supply of liquefied natural gas process technology and equipment, and globally provides turbomachinery, membrane systems and cryogenic containers.
The company had fiscal 2022 sales of $12.7 billion from operations in over 50 countries and has a current market capitalization of about $65 billion. More than 21,000 passionate, talented and committed employees from diverse backgrounds are driven by Air Products’ higher purpose to create innovative solutions that benefit the environment, enhance sustainability and reimagine what's possible to address the challenges facing customers, communities, and the world. For more information, visit www.airproducts.com or follow us on LinkedIn, X, Facebook or Instagram.
Authors Notes:
Stuart Devereux is currently a Hydrogen Safety and Response associate tutor with Ricardo. With previous careers in secondary school science education and UK Fire and Rescue, Stuart has a keen interest in safe use of hydrogen as a future fuel and educating the supply chain on the benefits and risks as well as managing hydrogen incident response.
Hector Wilson is the H2 for Mobility, Energy Transition & Sustainability Operations Lead for Air Products with 20+ years of gas and process engineering experience. Hector is developing the operational strategy for H2fMET for both “Blue” and “Green” hydrogen.
References
- EIGA DOC 06/02/E Safety in Storage, handling and distribution of liquid hydrogen
- Liquid Hydrogen: A review on liquefaction, Storage, Transportation and safety. Muhammad Aziz. Energies article September 2021
- Chemistry, the central science. Theodore Brown, Eugene LeMay. Prentice Hall publishing 1977
- How the world really works. Vaclav Smil. Penguin Publishing 2022
- Liu, Y.; Liu, Z.; Wei, J.; Lan, Y.; Yang, S.; Jin, T. Evaluation and prediction of the safe distance in liquid hydrogen spill accident. 2021
- Air Products
- Chart Industries Inc
- Big Chemical Encyclopedia
Image sources:
- www.geeksforgeeks.org
- www.chartindustries.com with thanks to Peter Gerstl (Director of Hydrogen Sales)
- www.airproducts.co.uk