How will e-motors evolve in the coming decade?
Electric drivelines are a cost efficient and sustainable solution for passenger and commercial vehicles, with one relatively small component playing a significant part in their evolution – the e-motor.
In an electric vehicle, the e-motor can operate as a motor and generator to provide propulsion power and regenerative braking. This type of operation requires control, robustness and in the case of an EV, helps maximise vehicle range and energy consumption. The e-motor response and efficiency will also directly affect smoothness, sound quality and acceleration.
How do electric motors work in electric vehicles?
In simple terms, the battery stores electrical energy, which is converted by the inverter to power the motor at the right speed and torque to the gears and then the wheels. The motor speed and torque vary with the electrical supply to the stator - the stationary portion of the electric generator or motor.
This is converted to a rotating magnetic field, which interacts with the rotor to produce torque and drive the EV. This process is controlled by the accelerator pedal, with response from the driveline acting as sensory input to the driver.
But what happens when the driver takes their foot off the accelerator? The EV momentum drives the transmission, providing torque to the e-motor rotor - the magnetic field interaction produces electricity. This electrical energy is converted by the inverter at the right DC voltage to be stored in the battery. This is regenerative braking and is similar to Internal Combustion Engine braking, but in this case the energy is not lost, but restored to the battery.
E-Motors have tremendous design flexibility, however, there isn’t a dominating technology that meets the needs of all EVs.
Types of Electric Motor Technology
Presently, there are four types of primary motor technology options, each with their own characteristics, including pros and cons:
- An Induction Motor, as used by Tesla and other vehicles, is a robust, low cost and fairly efficient option. Without a permanent magnet rotor, a magnetic field is produced by induction from the stator magnetic field. The power input from the battery can be converted into torque to help with quicker acceleration.
- A Synchronous Reluctance Motor is similarly robust as an induction motor but comes at a lower cost and is free from permanent magnets. The difference is that it operates using reluctance (think of magnetic resistance), where the rotor aligns to the stator magnetic field. The Alumotor (pictured below) is one such example of a Synchronous Reluctance Motor, which Ricardo is developing as a consortium of supply chain partners and academia.
- An Interior Permanent Magnet Motor is the most common topology. It has a has superb power density, torque, and efficiency. However, it comes with major drawbacks – it uses rare earth magnets, can be expensive and can be demagnetised or degraded due to high temperatures or a short-circuit.
- An Axial Flux Motor has a rotating and stationary magnetic field at 90 degrees to the radial flux motor, with the main flux paths in the axial direction. Since its aspect ratio is totally different, with a larger outer diameter than axial length, it has some advantages in that it can be packaged to the advantage of some applications. It has high torque density and can have a relatively immune air gap to external radial forces, making it a good option for applications such as propulsion motors and wind turbines.
Future trends for electric motors
Future trends for e-motors will concentrate on improving efficiency, better packaging and reducing capital costs. To improve efficiency, we may see the creation of hybrid motors, combining features from internal permanent magnets and synchronous reluctance motors, boosting efficiency but at moderate cost impact. Future designs and applications must be commercially viable if they are to be successful and an attractive proposition to OEMs and Tier 1 suppliers.
Improving sustainability of e-motors will also be an important factor and is set to remain one the of biggest challenges that manufacturers will face in the coming decade. The focus will be on ensuring the sustainabiliy of materials and minimising the use of energy and resources in the manufacturing process. However, it is necessary for OEMs to consider the full lifecycle of the product, including how the packaging and intergration of the e-motor can lower the overall environmental impact of this component.
How can OEMs improve the sustainability of their electric motors?
A focus on the reduction in the use of rare earth materials, such as Neodymium and Dysprosium, and non-recoverable materials will be essential. For every one tonne of rare earth materials mined, one and half tonnes of radioactive waste is created, and two hundred tonnes of water used. They also pose significant supply chain and commercial risk – 85% of rare earth materials are mined in China, so there’s a long supply chain involved and it’s subject to price volatility, including from exchange rates and government price setting.
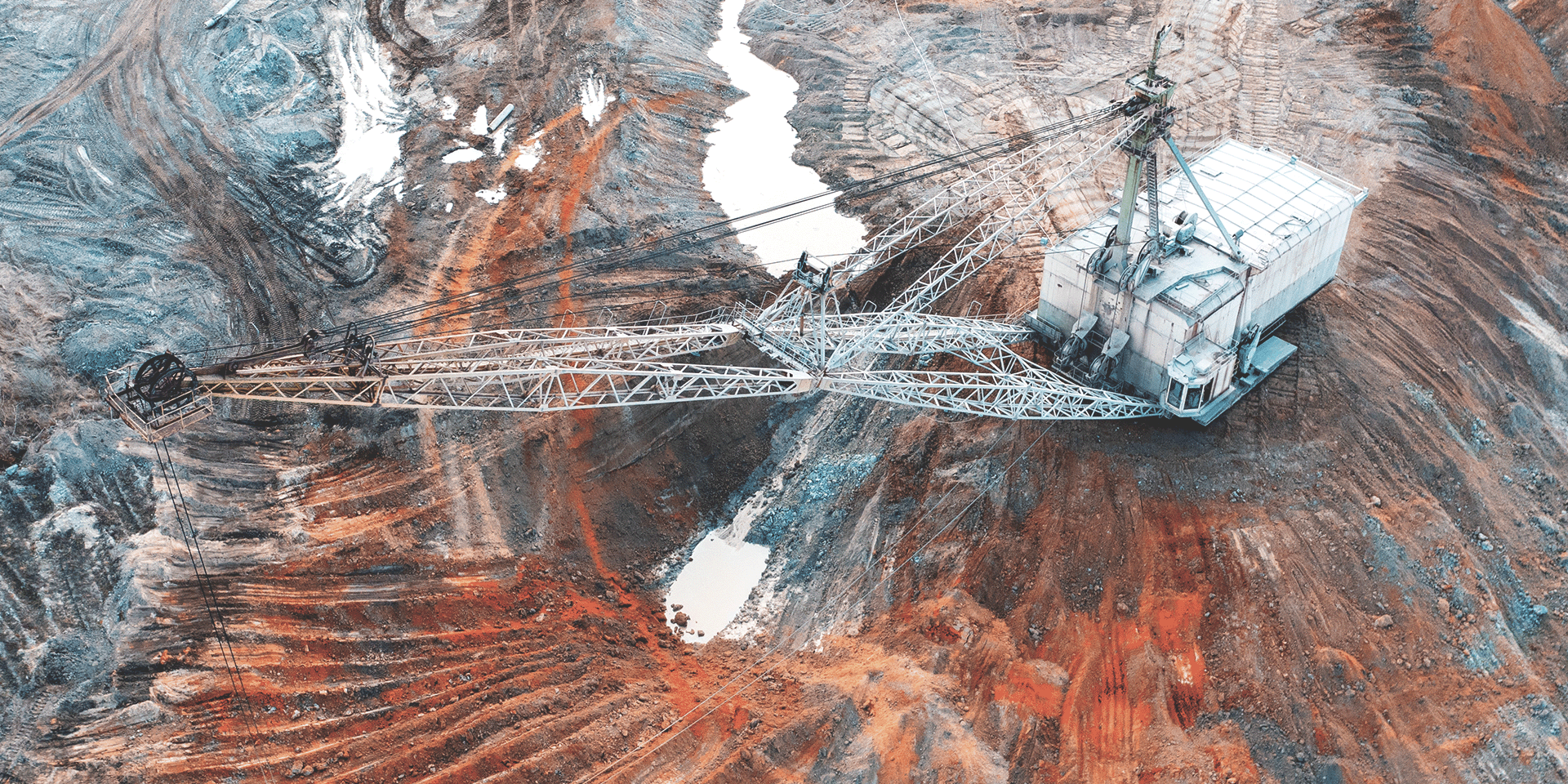
Looking more broadly at the packaging and integration of the e-motor, there are a number of methodologies which can be explored to reduce the environmental impact of the component and the electric vehicle as a whole. These include:
- Greater use of low weight materials such as aluminium and composites to improve vehicle efficiency
- Closer power electronic integration and a sympathetic control system to improve efficiency and power integration
- Improving high voltage architecture to enable the use of smaller conductors by reducing conduction losses
- Advancements in oil cooling technology, linked to improvements in thermal management
- Development of higher speed e-machines and a reduction in their size
Innovation is critical to driveline progression, and should involve a holistic approach to materials, integration, and thermal management – this will be important to providing a high impact development that delivers value.
Ricardo experts are working to accelerate client developments in the e-motor space, providing confidence for businesses in their investment into technology, production lines and supply chains. The technology investment that Ricardo has made allows clients to make decisions and benefit from competitive advantage, resulting in them being quicker to market and lowering the cost of development. Providing evidence for production line investment, including market and customer expectations, allows clients to make informed and better decisions, technically and commercially.
As OEMs and Tier 1 suppliers continue to transition to low carbon transport solutions, our differentiator is that we have research, development, and collaborative projects to call upon that provide insight into power electronics. Our future proofing technology ensures that we meet the targets and requirements set out by the APC and the US Department of Energy roadmap. As a result, we are at the forefront of design and engineering for cost, reliability, robustness, and importantly environmental development.
A blog by Dragica Kostic-Perovic