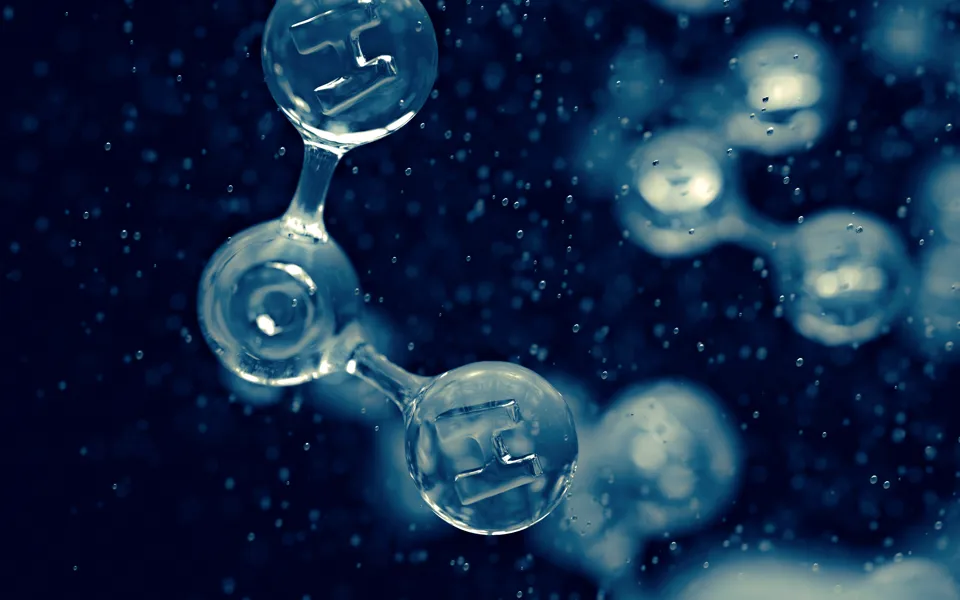
Sparking conversations in liquid hydrogen: Q&A with Temoc Rodriguez
27 Jul 2023
Q: Hi Temoc, let's start with an introduction to yourself
Temoc Rodriguez: Hi, I’m Temoc and my role at Ricardo is a Global Technical Expert in electronics systems. I joined Ricardo in 2021 after 20 years in various industries, from renewable power generation to oil & gas, industrial, and more recently aerospace.
I’m passionate about all things electrical and have seen the potential to run organisations and businesses more efficiently through the exploitation of advanced power electronics and technologies.
What sparked your career in electrical engineering?
Temoc Rodriguez: Ever since I can remember I’ve been interested in how electronics operate. I’m sure we can all relate to basic mechanics in bicycles and old vehicles, but once electronics are involved, it becomes a dark art,. I wanted to understand that “dark art”. Throughout my education, I focused on power electronics as that’s what enables things to move. I went on to complete a Bachelors, a Master’s, and a Ph.D. all in electrical engineering with specialisms in power electronics.
BACKGROUND AND BASICS:
Q) Can you provide a brief overview of the concept of liquid hydrogen cooling in electric propulsion systems?
Temoc Rodriguez: Recently I’ve been involved in leading a hydrogen fuel cell power system for a demonstrator aircraft, where we used compressed gaseous hydrogen as the energy source. However, the industry recognises that hydrogen will have to be liquified to truly make an impact in the mission range. Once hydrogen is in liquid form, it’ll have a cryogenic temperature of 20 Kelvin (-253 degrees Centigrade).
Take aircraft for example, we’re always looking to reduce the mass and volume of systems, so I figured by replacing the propulsion unit cooling system with a direct heat rejection into the liquid hydrogen that’s already available onboard the aircraft, we could save a lot of mass and volume.
Q) What are the main advantages of using liquid hydrogen as a cooling medium for electric propulsion systems?
Temoc Rodriguez: There are several advantages.
- The dedicated propulsion unit cooling system is removed, which translates to mass, volume, power, and system complexity reductions
- Cooling the propulsion inverter and electric machine to cryogenic temperatures will improve its efficiency as conduction ohmic losses are greatly reduced.
Q) How does liquid hydrogen cooling compare to other cooling methods in terms of efficiency and performance?
Temoc Rodriguez: In the research Ricardo conducted, we used a 250kW propulsion system as a benchmark for the analysis. Ricardo has ready-to-go technologies for hydrogen fuel cell systems and electric propulsion units, we know the technologies inside and out, plus have high confidence in what can be achieved.
As our research at Oxford University demonstrates, the inverter design based on Gallium Nitride semiconductors has exceptional characteristics at cryogenic temperatures compared to other semiconductors like Silicon Carbide. At this temperature, the inverter conduction losses are reduced by eight times, the overall efficiency moves up from 98% to 99.3%.
In the electric motor, the efficiency increases from around 96.5% to 97.5%. Similarly, we can use this effect to put more current through the machine and increase its power density.
TECHNICAL ASPECTS:
Q: Could you explain the thermal properties of liquid hydrogen and how it makes it suitable for cooling electric propulsion systems?
Temoc Rodriguez: The latent heat of vaporisation of hydrogen is much lower than water/glycol, which is conventionally used for cooling purposes. So we needed to find out if we could use hydrogen as a coolant Through Computer Fluid Dynamics and clever mechanical design, we demonstrated that it was possible to achieve this with ample margin. In fact, the challenge turned on its head, as we needed to ensure that we could heat the hydrogen above zero degrees Centigrade to prevent water from freezing at the inlet of the fuel cells.
Q: What are the key challenges associated with implementing liquid hydrogen cooling in electric propulsion systems?
Temoc Rodriguez: Generally, liquid hydrogen is used in industrial and medical applications, where space and mass are not a concern. For mobility, especially aerospace, we need to ensure that the benefits of using liquid hydrogen are not outweighed by the need for bulky and heavy components, meaning we need to design all these components from first principles.
I would say the main challenge is to handle the large thermal gradient between the liquid hydrogen (-253 degrees Centigrade) and the surrounding environment (20 to 60 degrees Centigrade).
Q: Can you describe the design considerations that need to be taken into account when incorporating liquid hydrogen cooling into an electric propulsion system?
Temoc Rodriguez: Yes, the cold plates are highly engineered to maximise heat transfer to the liquid hydrogen, Ricardo has trialled dozens of concepts selecting effective solutions.
The layout and placement of the cold plate for the inverter and the cooling jacket for the motor is critical, in the case of the inverter, we want to thermally isolate the cold plate from the enclosure and the conventional electronics, which can only operate down to -55 degrees Centigrade.
In the case of the motor, we need to prevent the freezing of water, carbon dioxide and oxygen present in the surrounding ambient. As the hydrogen flows around the jacket it will warm up considerably until it reaches near 0 degrees Centigrade at the outlet.
INTEGRATION AND IMPLEMENTATION:
Q: How does the integration of a liquid hydrogen cooling system impact the overall design and layout of an electric propulsion system?
Temoc Rodriguez: The propulsion system has to be placed close to the fuel cells and tanks to avoid long pipe runs of cryogenic hydrogen as they need to be thermally isolated from the surrounding environment. Another aspect that needs close attention is the safety of the system. In our hydrogen fuel cell systems, we have safety monitoring systems ensuring the system operates within acceptable parameters, monitoring any abnormal leakage of hydrogen.
ENVIRONMENTAL IMPACT AND SUSTAINABILITY:
Q: What are the environmental considerations when using liquid hydrogen as a cooling medium? How does it align with sustainability goals?
Temoc Rodriguez: Most hydrogen today is obtained through gas reforming methods as a by-product of oil and gas operations. In more recent years, there’s been a big push towards “green hydrogen” generated from electrolysers powered by renewable energy, this is the fuel that we should be using to decarbonise our economies. As the process is less than 50% efficient, unfortunately, this comes with something called an efficiency penalty, this is one of the reasons why Ricardo continues to promote battery-powered vehicles where it makes sense, such as passenger vehicles. However, some mobility sectors cannot work with batteries due to their weight, volume, or charge time.
Q: How do the lifecycle emissions and environmental impacts of a liquid hydrogen-cooled electric propulsion system compares to alternative cooling methods?
Temoc Rodriguez: The propulsion unit will run at higher efficiency, which by definition means it requires less energy to complete a mission compared to the conventionally cooled system. The concept we are proposing here only works for vehicles that require a hydrogen fuel cell system and an electric propulsion unit.
OPERATIONAL AND MAINTENANCE ASPECTS:
Q: What maintenance and operational challenges might arise with a liquid hydrogen cooling system, and how are they typically addressed?
Temoc Rodriguez: Hydrogen systems need to be regularly maintained, including inspections of the materials and pressure-proofing of the system. As these are already in place for the hydrogen fuel cell system, no additional measures would be required for the propulsion unit, we’d simply add steps to the existing maintenance tasks to also check the cold plate and cooling jacket.
FUTURE TRENDS AND INNOVATIONS:
Q: Are there any ongoing research or developments in the field of liquid hydrogen cooling for electric propulsion that you find particularly promising or exciting?
Temoc Rodriguez: Since starting research two years ago at Oxford University, we learned that others started looking into this, which is extremely encouraging as it validates the work and that other people have identified the synergies and benefits of this Ricardo-generated approach.
Q: How do you envision the role of liquid hydrogen cooling evolving in future electric propulsion systems?
Temoc Rodriguez: It will take time to mature and deploy, particularly in the aviation sector as the hurdles to demonstrate a safe system are onerous.
COLLABORATION AND INDUSTRY TRENDS:
Q: Can you share insights on collaboration and partnerships within the industry to advance the adoption of liquid hydrogen cooling in electric propulsion systems?
Temoc Rodriguez: Our next step will be to identify industry partners and funding calls to develop the technology further into a physical demonstrator, building a system is the most effective way to truly identify all the challenges and their solutions. Ricardo’s expertise lies in propulsion system technologies so we would be looking for OEMs in the aviation, marine, or rail sectors in addition to liquid hydrogen storage and handling companies.
Q: What trends do you observe in terms of industry interest and investment?
Temoc Rodriguez: The aviation and marine sectors have already identified liquid hydrogen as the long-term solution to fuel their platforms. We now need to work with them to demonstrate the benefits of the synergy between the cryogenic energy storage and the cooling needs of the propulsion unit.
Temoc is currently leading the development of a hydrogen fuel cell system for aerospace propulsion and research on high-power Gallium Nitride propulsion inverters.
He will be presenting at the electric and hybrid aerospace expo that coincides with the hydrogen technology expo.
Presentation: Liquid hydrogen cooling of electric propulsion system
Liquid hydrogen fuel cells are earmarked as one of the solutions to decarbonise long-haul transport including aviation. Liquid hydrogen can be used to reject the heat generated by losses in the electric powertrain. To achieve this, the liquid hydrogen is first circulated through the cold plate of the propulsion inverter and then through the cooling jacket of the electric machine. The outgoing hydrogen is then fed to the fuel cell system. This results in a simpler, lighter, and more efficient system. The design of the inverter cold plate and the electric machine cooling jacket and their operation are presented.